|
The Thread/Tap capability creates
threads or taps, depending on the cylindrical entity of interest. This task shows you how to thread
a cylindrical pad. |
|
Open the Thread.CATPart
document.. |
|
1. |
Click the Thread/Tap icon
. The
Thread/Tap
Definition dialog box is displayed.
|
|
|
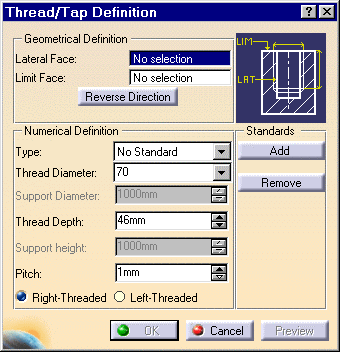
|
|
2. |
Select the cylindrical surface you wish to
thread, that is Face.1. |
|
|
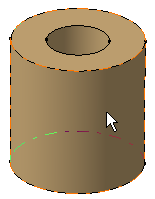
|
|
3. |
Select the upper face as the limit face. Limit faces must
be planar.
The application previews the thread. |
|
|
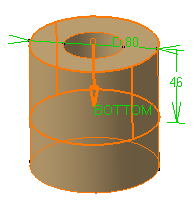
|
|
|
In the dialog box, the Geometrical Definition
frame displays the name of the faces you have selected. The Reverse
Direction button (as well as the arrow in the geometry area) lets you
reverse the thread direction if needed. |
|
|
The Numerical Definition frame provides three different
thread types:
|
|
|
 | Metric Thin Pitch: AFNOR standard |
Refer to (NF E03-053-1970). This normative reference is linked to NF E03-051-1982)
The application uses the minimum standard values.
Nominaldiam |
Pitch |
Minordiam |
M |
8.0 |
1.0 |
6.917 |
|
9.1 |
1.0 |
7.917 |
|
10.0 |
1.25 |
8.647 |
|
12. |
1.25 |
10.647 |
|
14.0 |
1.5 |
12.376 |
|
16.0 |
1.5 |
14.376 |
|
18.0 |
1.5 |
16.376 |
|
20.0 |
1.5 |
18.376 |
|
22.0 |
1.5 |
20.376 |
|
24.0 |
2.0 |
21.835 |
|
27.0 |
2.0 |
24.835 |
|
30.0 |
2.0 |
27.835 |
|
33.0 |
2.0 |
30.835 |
|
36.0 |
3.0 |
32.752 |
|
39.0 |
3.0 |
35.752 |
|
|
|
|
 | Metric Thick Pitch: AFNOR standard |
Refer to (NF E03-053-1970). This normative reference is linked to NF E03-051-1982)
The application uses the minimum standard values. |
|
|
Nominaldiam
|
Pitch |
Minordiam |
M |
1 |
0.25 |
0.729 |
|
1.1 |
0.25 |
0.829 |
|
1.2 |
0.25 |
0.829 |
|
1.4 |
0.3 |
1.075 |
|
1.6 |
0.35 |
1.221 |
|
1.8 |
0.35 |
1.221 |
|
2.0 |
0.4 |
1.567 |
|
2.2 |
0.45 |
1.713 |
|
2.5 |
0.45 |
2.013 |
|
3.0 |
0.5 |
2.459 |
|
3.5 |
0.6 |
2.850 |
|
4.0 |
0.7 |
3.242 |
|
4.5 |
0.75 |
3.688 |
|
5.0 |
0.8 |
4.134 |
|
6.0 |
1.0 |
4.917 |
|
7.0 |
1.0 |
5.917 |
|
8.0 |
1.25 |
6.647 |
|
9.0 |
1.25 |
7.647 |
|
10.0 |
1.5 |
8.376 |
|
12.0 |
1.75 |
10.106 |
|
14.0 |
2.0 |
11.835 |
|
16.0 |
2.0 |
13.835 |
|
18.0 |
2.5 |
15.294 |
|
20.0 |
2.5 |
17.294 |
|
22.0 |
2.5 |
19.294 |
|
24.0 |
3.0 |
20.752 |
|
27.0 |
3.0 |
23.752 |
|
30.0 |
3.5 |
26.211 |
|
33.0 |
3.5 |
29.211 |
|
36.0 |
4.0 |
31.670 |
|
39.0 |
4.0 |
34.670 |
|
42.0 |
4.5 |
37.129 |
|
45.0 |
4.5 |
40.129 |
|
48.0 |
5.0 |
42.587 |
|
52.0 |
5.0 |
46.587 |
|
56.0 |
5.5 |
50.046 |
|
60.0 |
5.5 |
54.046 |
|
64.0 |
6.0 |
57.505 |
|
68.0 |
6.0 |
61.505 |
|
72.0 |
6.0 |
65.505 |
|
76.0 |
6.0 |
69.505 |
|
80.0 |
6.0 |
73.505 |
|
85.0 |
6.0 |
78.505 |
|
90.0
|
6.0 |
83.505 |
|
|
|
4. |
For the purposes of our scenario, keep No
Standard. As you are creating a thread, you cannot modify the thread
diameter value. If you were creating a tap, you could modify it. |
|
|
When creating taps, if you wish to use values already
defined in one of your files, click the Add button to access this file. A dialog box displays, in which you can navigate to reach the file
containing your own values. This file may be of one of the following
types:
 | Excel files (general format) |
 | Lotus files |
 | tabulated files (in Unix environment) |
For more about using predefined values, refer to Threaded
Holes, steps 7 and 8. The operating mode described in this task is
valid for threads and taps too. |
|
5. |
Enter 49 mm as the thread depth.
Note that the Support Diameter and Support height fields are grayed.
They are merely informative.
|
|
6. |
Enter 1.5 mm as the pitch value. The Pitch field defines the
distance between each crest. |
|
7. |
Check the Left-Threaded option. |
|
8. |
Click Preview.
Red lines provide a simplified representation of the
thread. |
|
|
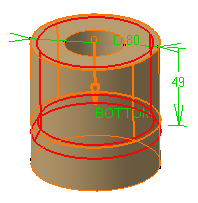
|
|
9. |
Click OK to confirm.
There is no
geometrical representation is the geometry area, but the
thread (identified as Thread.xxx) is added to the specification tree.
The corresponding icon is specific to this feature. |
|
|
Diameter, depth and pitch values appear below the Thread entity in
the specification tree. |
|
|
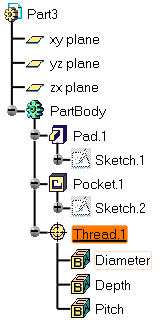
|
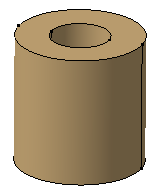
|
|
|
If you create a tap, CATIA identifies it as
Thread.XXX too in the specification tree, but displays a specific icon as
shown below: |
|
|
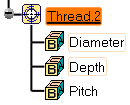
|
|
|
Notes
 | You can extract drawings from threads and taps
in the Generative Drafting workbench. For more, see Generative
Drafting User's Guide Version 5. |
 | You obtain a hole, not a tapped hole, by removing
a threaded cylinder from a body. |
|
|
|
Cavities on cylindrical surfaces
 | If the cavity is a hole, proceed using the options available in the
Hole Definition dialog box as described in Threaded
Holes. |
 | If the cavity is a groove or a pocket defined on a cylindrical
surface, you must use a plane tangent to the surface as the limit
face. |
|
|